|
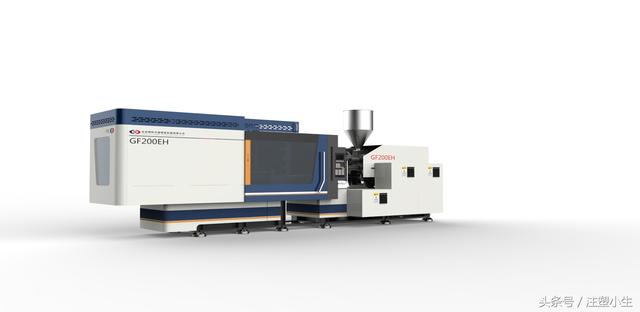
问题 可能成因 解决方法 小黑点熔胶筒内壁烧焦,胶块脱落1.清洗炮筒内壁(拆螺杆清小洗)2.用较硬胶料进入,以擦净炮筒内壁(小船坞机,如用清洗剂及亚加力等)3.避免胶料长时间受高温(料温不宜太高,储料不能太多,
黑点空气带来肮脏物或模腔腔内有空气引至1.封盖料斗2.胶料封闭好,保持干净3.增加或减低熔胶筒和模具温度,以改变胶料进入模腔的速度4.减低注塑压力或速度
黑色条纹1.料筒或螺杆不干净,原料不干净1.清理料筒及螺杆并小心处理胶料不受污染2.料筒能胶料局部过热2.使炮筒之每段受热圴匀3.冷胶料互相磨擦或与炮筒壁磨擦时烧焦3.A加入有外润滑剂的胶料 B胶料加小许白矿油 C增加炮筒后段温度4.射嘴过热烧焦胶料4.减低射嘴温度5.射嘴温度变化大5.采用恒温控制器控制电热
黄点 黄线 棕色条纹变色1.溶胶筒全面或局部过热1.A 减低温度 B减低螺杆转速 C减低回料背压2.胶料黏住炮筒内壁或射嘴以至烧2.清理射嘴或炮筒螺杆3.胶料在炮筒内停留时间过长3.缩短注塑周期4.炮筒内存有死角4.更换螺杆
产品哑白 原料潮湿烘干原料再生产
气泡模腔填料不足,原因:1.A制品切面厚,模腔壁上有突起线1.A 再设计模具B 注塑压力太低B 加大注塑压力C 注塑时间太长C 增加注塑时间D 入料不足 D 增加注塑速度及增加入水口阔度2.胶料潮湿2.模塑前胶粒避免受过大的温度变化及要干燥胶粒3.模具温度不均匀3.重新排列运水信道,使模具温度一致
破裂或龟裂1.填模太实1.A减低速度;B减低压国 C 缩短注射时间2.模温太低2.提高模温3.不适当的脱模设计如角度斜位及倒扣位3.修改工模4.顶针或环定不当4.再按放顶针让制品能顺利顶出工模5.再用料过多(拉粒水口)5.少用或不用拉粒或水口
产品尺寸性改变1.模塑情况不稳定1.A 调节操作情况,直至得到最大平稳操作B 视乎啤塑工人的操作情况而决定啤塑时间长短2.注塑条件与正常时不一致2.A 更正跟平常时不用的注塑条件B 检查注塑温度,压力 ,工模温度,模塑时间,入料,电压,3.在检查塑件时周围空气温度不固定3.A 保持周围空气温度固定B 在同一条件下测量及检查制品
漏胶1.胶料太热1.A 降低胶料温度B 减少螺杆转速和背压2.注塑压力过高2.A 降低压力B 减少枕压时间3.模具或射咀凸凹两面接触不良3.再次打磨模具唧嘴4.射台增压不够4.检查机台射台射增压系统
开模时射咀滴胶1.胶料过热1.A 降低炉咀温度B 降低料筒温度2.注塑料料不够干燥2.干燥胶料
流纹和塑面起波纹1.胶料不够热1.增加胶料温度2.模温不够热2.增加工模温度3.注射压力太低3.提高注射现象4.注射速度太低4.提高注塑速度5.浇口太小引致胶料在模腔内有喷射现象5.扩大浇口和降低注射压力6.塑品切面厚薄不均匀6.A设计塑件俾切面厚薄均一B去除制品上凸起的线条7.排气不足7.增加排气
塑料在浇口成层状1.模温太低1.升高电热、升高模温2.射速太慢2.提高注射速度3.注射压力不足3.提高注塑速度4.射胶时间过长4.缩短射胶时间5.胶料有杂质5.A清洁熔胶筒B避免混入其它塑料6.工模润滑剂过多6.清洁模面,用小量润滑剂(脱模剂)7.水口小7.调节水口大小,使其得到良好的压力控制水口四周有条纹料温过高,流速太快降低温度及注射速度啤塑周期需时过长1.料温度高易缩水1.A 降低温度B 减少螺杆旋转速度或背压2.工模温度过高2.降低模温3.模塑时间不稳定(工人问题)3.用计时表及加强管制工人的操作速度4.塑料融化的温度和所需时间不够4.增加温度和延长时间5.塑件较厚处冷却不足5.A 改变模内冷却水道位置B 用冷水机
产品变形1.注射压力太大1.减低注射压力2.保压时间过长2.减少保压时间3.前后模差太大3.使前且模温一致4.入水位设计不常4.再设计入水位置5.塑件切面厚度不均匀5.尽可能保持切面厚度均匀6.工模温度过低6.增高模温7.料温过低7.升高料温C注6和7即变相减压8.螺杆背压过高8.减少螺杆背压
塑件粘模1.注射压力或熔胶筒温度过高1.A 减低注射压力或机筒温度B 降低螺杆的旋转速度或螺杆背压2.过多入料2.减少入料3.注射时间过长3.减少注射时间4.工模冷却不足(塑件热膨胀)4.延长工模冷却时间5.塑件因收缩而粘在阳模上5.减少冷却时间,使前后模有不同温度6.模内塑件未冷硬6.延长保压并加强工模冷却7.工模内有倒扣位7.却除倒扣位,打磨抛光,增加脱兔 模部份的斜度8.模腔内深入部份空气压力小(真空状态)8.设立适宜的排气道9.工模内壁光洁度不够9.模腔壁再次抛光
夹纹1.料温太低1.升高料温2.模面有脱模剂等油渍2.抹干净工模壁,不喷脱模剂或少脱模剂3.熔溶位离入水位太远3.再设定入水位或再加几个对称的入水4.排气不良4.增设足够排气5.塑品切面厚薄转化大5.再设计塑件及设定适当的入水位置6.模温太低6.提高模温7.注塑压力低及速度慢7.升高注射压力或速度
塑件表面粗糙1.模温低1.提高模温2.注射压力低2.增加注射压力3.注射速度慢3.增加注射速度4.模壁有水份4.清洁和修理漏水裂痕或防止水汽在模壁凝洁5.用脱模剂过多5.不用或少用脱模剂6.使用过多的内或外润滑剂6.检查材料是适合和混料时减少矿油用量7.模表面粗糙7.再次抛光模壁
射胶不足1.熔胶管各段不够1.增加熔胶筒各段2.模温不够2.温度增加模温3.压力不足3.增加压力4.刚开机时射咀太冷4.多啤几啤或用火焰加热射咀5.模温不均一5.不用或少用脱模剂6.空气不能排出模腔(困气)6.增加排气道数目及尺码7.注射时间不够7.增加注射时间8.流入多模腔工模的熔胶流态不能适当平行8.修正平行情形9.浇口小9.扩大浇口10.模腔熔胶量比注塑机大10.用较大的注塑机
塑件表面光亮条纹1.料温不够1.提高熔胶筒温度2.模温低2.升高模温3.模内有水气3.加热干燥工模4.工模有污渍4.清洁工模5.转压转速位置不当5.调整适当的转压转速位置6.料内有湿气6.烘干胶料油温机利用热传导原理,将热传导油加热至适当温度,输送至成型机模具之管道内,加热模具至要求温度,并控制油温在要求温度范围内。适合模温要求高的成型。改善塑料制品的质量,亦可提高生产效益。
1
注塑件收缩凹陷的原因分析
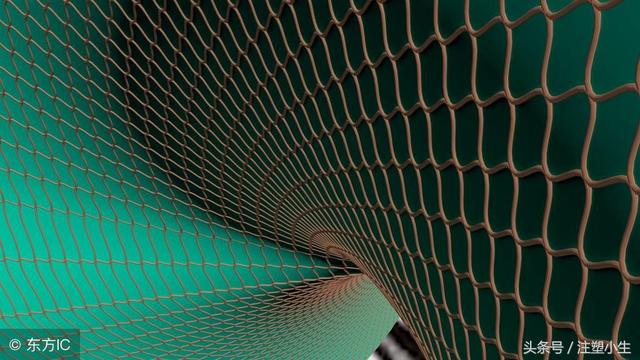
注塑成型过程中,制品收缩凹陷是比较常见的现象。造成这种情况的主要原因有:
机台方面
(1)射嘴孔太大造成融料回流而出现收缩,太小时阻力大料量不足出现收缩。
(2)锁模力不足造成飞边也会出现收缩,应检查锁模系统是否有问题。
(3)塑化量不足应选用塑化量大的机台,检查螺杆与料筒是否磨损。
模具方面
(1)制件设计要使壁厚均匀,保证收缩一致。
(2)模具的冷却、加温系统要保证各部份的温度一致。
(3)浇注系统要保证通畅,阻力不能过大,如主流道、分流道、浇口的尺寸要适当,光洁度要足够,过渡区要圆弧过渡。
(4)对薄件应提高温度,保证料流畅顺,对厚壁制件应降低模温。
(5)浇口要对称开设,尽量开设在制件厚壁部位,应增加冷料井容积。
塑料方面
结晶性的塑料比非结晶性塑料收缩历害,加工时要适当增加料量,或在塑料中加成换剂,以加快结晶,减少收缩凹陷。
加工方面
(1)料筒温度过高,容积变化大,特别是前炉温度,对流动性差的塑料应适当提高温度、保证畅顺。
(2)注射压力、速度、背压过低、注射时间过短,使料量或密度不足而收缩压力、速度、背压过大、时间过长造成飞边而出现收缩。
(3)加料量即缓冲垫过大时消耗注射压力,过小时,料量不足。
(4)对于不要求精度的制件,在注射保压完毕,外层基本冷凝硬化而夹心部份尚柔软又能顶出的制件,及早出模,让其在空气或热水中缓慢冷却,可以使收缩凹陷平缓而不那么显眼又不影响使用。
2
注塑件震纹的原因分析
PS等刚性塑料制件在其浇口附近的表面,以浇口为中心的形成密集的波纹,有时称为震纹。产生原因是熔体粘度过大而以滞流形式充模时,前端的料一接触到型腔表面便很快冷凝收缩起来,而后来的熔料又胀开已收缩的冷料继续前进过程的不断交替使料流在前进中形成了表面震纹。
解决办法
(1)提高料筒温度特别是射嘴温度,还应提高模具温度。
(2)提高注射压力与速度,使其快速充模型腔。
(3)改善流道、浇口尺寸,防止阻力过大。
(4)模具排气要良好,要设置足够大的冷料井。
(5)制件不要设计得过于薄。
3
注塑件肿胀和鼓泡的原因分析
有些塑料制件在成型脱模后,很快在金属嵌件的背面或在特别厚的部位出现肿胀或鼓泡。这是因为未完全冷却硬化的塑料在内压罚的作用下释放气体膨胀造成。
解决办法
1.有效的冷却。降低模温,延长开模时间,降低料的干燥与加工温度。
2.降低充模速度,减少成形周期,减少流动阻力。
3.提高保压压力和时间。
4.改善制件壁面太厚或厚薄变化大的状况。
4
注塑件开裂的原因分析
加工方面
(1)加工压力过大、速度过快、充料愈多、注射、保压时间过长,都会造成内应力过大而开裂。
(2)调节开模速度与压力防止快速强拉制件造成脱模开裂。
(3)适当调高模具温度,使制件易于脱模,适当调低料温防止分解。
(4)预防由于熔接痕,塑料降解造成机械强度变低而出现开裂。
(5)适当使用脱模剂,注意经常消除模面附着的气雾等物质。
(6)制件残余应力,可通过在成型后立即进行退火热处理来消除内应力而减少裂纹的生成。
模具方面
(1)顶出要平衡,如顶杆数量、截面积要足够,脱模斜度要足够,型腔面要有足够光滑,这样才防止由于外力导致顶出残余应力集中而开裂。
(2)制件结构不能太薄,过渡部份应尽量采用圆弧过渡,避免尖角、倒角造成应力集中。
(3)尽量少用金属嵌件,以防止嵌件与制件收缩率不同造成内应力加大。
(4)对深底制件应设置适当的脱模进气孔道,防止形成真空负压。
(5)主流道足够大使浇口料未来得及固化时脱模,这样易于脱模。
(6)主流道衬套与喷嘴接合应当防止冷硬料的拖拉而使制件粘在定模上。
材料方面
(1)再生料含量太高,造成制件强度过低。
(2)湿度过大,造成一些塑料与水汽发生化学反应,降低强度而出现顶出开裂。
(3)材料本身不适宜正在加工的环境或质量欠佳,受到污染都会造成开裂。
机台方面
注塑机塑化容量要适当,过小塑化不充分未能完全混合而变脆,过大时会降解。
5
注塑件气泡的原因分析
气泡(真空泡)的气体十分稀薄属于真空泡。一般说来,如果在开模瞬间已发现存在气泡是属于气体干扰问题。真空泡的形成是由于充注进塑料不足或压力较低。在模具的急剧冷却作用下,与型腔接角的燃料牵拉,造成体积损失的结果。
解决方法
(1)提高注射能量:压力、速度、时间和料量,并提高背压,使充模丰满。
(2)增加料温流动顺畅。降低料温减少收缩,适当提高模温,特别是形成真空泡部位的局部模温。
(3)将浇口设置在制件厚的部份,改善喷嘴、流道和浇口的流动状况,减少压务的消耗。
(4)改进模具排气状况。
6
注塑件翘曲变形的原因分析
注塑制品变形、弯曲、扭曲现象的发生主要是由于塑料成型时流动方向的收缩率比垂直方向的大,使制件各向收缩率不同而翘曲,又由于注射充模时不可避免地在制件内部残留有较大的内应力而引起翘曲,这些都是高应力取向造成的变形的表现。所以从根本上说,模具设计决定了制件的翘曲倾向,要通过变更成型条件来抑制这种倾向是十分困难的,最终解决问题必须从模具设计和改良着手。这种现象的主要有以下几个方面造成:
模具方面
(1)制件的厚度、质量要均匀。
(2)冷却系统的设计要使模具型腔各部分温度均匀,浇注系统要使料流对称避免因流动方向、收缩率不同而造成翘曲,适当加粗较难成型部份的分流道、主流道,尽量消除型腔内的密度差、压力差、温度差。
(3)制件厚薄的过渡区及转角要足够圆滑,要有良好的脱模性,如增加脱模余度,改善模面的抛光,顶出系统要保持平衡。
(4)排气要良好。
(5)增加制件壁厚或增加抗翘曲方向,由加强筋来增强制件抗翘曲能力。
(6)模具所用的材料强度不足。
塑料方面
结晶型比非结晶型塑料出现的翘曲变形机会多,加之结晶型塑料可利用结晶度随冷却速度增大而降低,收缩率变小的结晶过程来矫正翘曲变形。
加工方面
(1)注射压力太高,保压时间太长,熔料温度太低速度太快会造成内应力增加而出现翘曲变形。
(2)模具温度过高,冷却时间过短,使脱模时的制件过热而出现顶出变形。
(3)在保持最低限度充料量下减少螺杆转速和背压降低密度来限制内应力的产生。
(4)必要时可对容易翘曲变形的制件进行模具软性定形或脱模后进行退米处理。
7
注塑件色条色线色花分析
这种缺陷的出现主要是采用色母粒着色的塑料制件较常出现的问题,虽然色母粒着色在色型稳定性、色质纯度和颜色迁移性等方面均优于干粉着色、染浆着色,但分配性,亦即色粒在稀释塑料在混合均匀程度却相对较差,制成品自然就带有区域性色泽差异。
解决办法
(1)提高加料段温度,特别是加料段后端的温度,使其温度接近或略高于熔融段温度,使色母粒进入熔融段时尽快熔化,促进与稀释均匀混合,增加液态混合机会。
(2)在螺杆转速一定的情况下,增加背压压力使料筒内的熔料温度、剪切作用都得到提高。
(3)修改模具,特别浇注系统,如浇口过宽,融料通过时,紊流效果差,温度提升不高,于是就不均匀,色带模腔,应予改窄。
8
注塑件透明缺陷的原因分析
熔斑、银纹、裂纹聚苯乙烯、有机玻璃的透明制件,有时候透过光线可以看到一些闪闪发光的细丝般的银纹。这些银纹又称烁斑或裂纹。这是由于拉应力的垂直方向产生了应力,使用权聚合物分子发重型流动取向而与未取向部分折完率差异表现出来。
解决办法
(1)消除气体及其它杂质的干扰,对塑料充分干燥。
(2)降低料温,分段调节料筒温度,适当提高模温。
(3)增加注射压力,降低注射速度。
(4)增加或减少预塑背压压力,减少螺杆转速。
(5)改善流道及型腔排气状况。
(6)清理射嘴、流道和浇口可能的堵塞。
(7)缩短成型周期,脱模后可用退火方法消除银纹:对聚苯乙烯在78℃时保持15分钟,或50℃时保持1小时,对聚碳酸酯,加热到160℃以上保持数分钟。
9
注塑件颜色不均的原因分析
造成注塑制品颜色不均的主要原因及解决方法如下:
(1)着色剂扩散不良,这种情况往往使浇口附近出现花纹。
(2)塑料或着色剂热稳定性差,要稳定制件的色调,一定要严格固定生产条件,特别是料温、料量和生产周期。
(3)对结晶型塑料,尽量使制件各部分的冷却速度一致,对于壁厚差异大的制件,可用着色剂来掩蔽色差,对于壁厚较均匀的制件要固定好料温和模温。
(4)制件的造型和浇口形式,位置对塑料充填情况有影响,使制件的某些局部产生色差,必要时要进行修改。
10
颜色及光泽缺陷的原因分析
正常情况下,注塑制件表面具有的光泽主要由塑料的类型、着色剂及模面的光洁度所决定。但经常也会因为一些其他的原因造成制品的表面颜色及光泽缺陷、表面暗色等缺陷。造成这种原因及解决方法分析如下:
(1)模具光洁度差,型腔表面有锈迹等,模具排气不良。
(2)模具的浇注系统有缺陷,应增大冷料井,增大流道、抛光主流道、分流道和浇口。
(3)料温与模温偏低,必要时可用浇口局部加热办法。
(4)加工压力过低、速度过慢、注射时间不足、背压不足,造成密实性差而使表面暗色。
(5)塑料要充分塑化,但要防止料的降解,受热要稳定,冷却要充分,特别是厚壁的。
(6)防止冷料进入制件,必要时改用自锁式弹簧或降低喷嘴温度。
(7)使用的再生料过多,塑料或着色剂质量差,混有水汽或其它杂质,使用的润滑剂质量差。
(8)锁模力要足够。
11
注塑件银纹的原因分析
注塑制品银纹,包括表面气泡和内部气孔。造成缺陷的主要原因是气体(主要有水汽、分解气、溶剂气、空气)的干扰。具体原因分析如下:
机台方面
(1)料筒、螺杆磨损或过胶头、过胶圈存在料流死角,长期受热而分解。
(2)加热系统失控,造成温度过高而分解,应检查热电偶、发热圈等加热元件是否有问题。螺杆设计不当,造成个解或容易带进空气。
模具方面
(1)排气不良。
(2)模具中流道、浇口、型腔的磨擦阻力大,造成局部过热而出现分解。
(3)浇口、型腔分布不平衡,冷却系统不合理都会造成受热不平衡而出现局部过热或阻塞空气的通道。
(4)冷却通路漏水进入型腔。
塑料方面
(1)塑料湿度大,添加再生料比例过多或含有有害性屑料(屑料极易分解),应充分干燥塑料及消除屑料。
(2)从大气中吸潮或从着色剂吸潮,应对着色剂也进行干燥,最好在机台上装干燥器。
(3)塑料中添加的润滑剂、稳定剂等的用量过多或混合不均,或者塑料本身带有挥发性溶剂。混合塑料受热程度难以兼顾时也会出现分解。
(4)塑料受污染,混有其它塑料。
加工方面
(1)设置温度、压力、速度、背压、熔胶马达转速过高造成分解,或压力、速度过低,注射时间、保压不充分、背压过低时,由于未能获得高压而密度不足无法熔解气体而出现银纹,应设置适当的温度、压力、速度与时间及采用多段注射速度。
(2)背压低、转速快易使空气进入料筒,随熔料进入模具,周期过长时融料在料筒内受热过长而出现分解。
(3)料量不足,加料缓冲垫过大,料温太低或模温太低都影响料的流动和成型压力,促使气泡的生成。
12
注塑件有熔接缝的原因分析
熔融塑料在型腔中由于遇到嵌件孔洞、流速不连贯的区域、充模料流中断的区域而以多股形式汇合时,因不能完全熔合而产生线性的熔接缝。此外在发生浇口喷射充模也会生成熔接缝,熔接缝处的强度等性能很差。主要原因分析如下:
加工方面
(1)注射压力、速度过低,料筒温度、模温过低,造成进入模具的融料过早冷却而出现熔接缝。
(2)注射压力、速度过高时,会出现喷射而出现熔接缝。
(3)应增加转速,增加背压压力使塑料粘度下降,密度增加。
(4)塑料要干燥好,再生料应少用,脱模剂用量太多或质量不好也会出现熔接缝。
(5)降低锁模力,方便排气。
模具方面
(1)同一型腔浇口过多,应减少浇口或对称设置,或尽量靠近熔接缝设置。
(2)熔接缝处排气不良,应开设排气系统。
(3)浇道过大、浇注系统尺寸不当,浇口开设尽量避免熔体在嵌件孔洞周围流动,或尽量少用嵌件。
(4)壁厚变化过大,或壁厚过薄,应使制件的壁厚均匀。
(5)必要时应在熔接缝处开设熔合井使熔接缝脱离制件。
塑料方面
(1)对流动性差或热敏性的塑料应适当添加润滑剂及稳定剂。
(2)塑料含的杂质多,必要时要换质量好的塑料。 |
|